In the competitive automotive industry, optimised CAD design for automotive pistons plays a crucial role in improving engine performance and fuel efficiency. Optimised CAD design for automotive pistons plays a crucial role in achieving these goals. Optimising piston design not only enhances engine efficiency but also boosts reliability and longevity. At Transient Geometry, we specialise in providing automated solutions that streamline the design process of pistons and other engine components, helping manufacturers stay ahead of the curve.
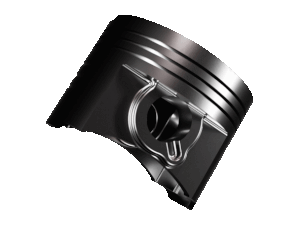
Optimised CAD for Automotive Pistons: Impact on Engine Performance
Understanding Piston Dynamics
Pistons are the workhorses of internal combustion engines, converting the energy from fuel combustion into mechanical motion. Their design significantly impacts several aspects of engine performance:
- Thermal Efficiency: An optimised piston shape ensures better combustion, leading to improved thermal efficiency and reduced fuel consumption.
- Mechanical Strength: Pistons must withstand extreme pressures and temperatures. A well-designed piston resists deformation and wear, enhancing engine durability.
- Weight Considerations: Reducing piston weight decreases the reciprocating mass, allowing for higher engine speeds and improved acceleration without compromising structural integrity.
Challenges in Traditional Piston Design
Conventional piston design methods often involve extensive manual calculations and iterative prototyping. Engineers typically spend countless hours tweaking designs to meet performance criteria, which introduces several challenges:
- Time-Consuming Processes: Manual design adjustments and physical prototyping extend development cycles, delaying time-to-market.
- Limited Optimisation: Exploring multiple design variables simultaneously is difficult, limiting the potential for finding the most efficient design.
- Higher Costs: Prolonged development and testing phases increase overall project expenses.
These challenges highlight the need for a more efficient approach to piston design that leverages modern technology.
Embracing Optimised CAD Design for Automotive Pistons
CAD Tools for Optimised Piston Design
Optimised CAD design for automotive pistons allows engineers to integrate material properties and simulate real-world conditions efficiently. By utilising advanced CAD software, engineers can:
- Simulate Real-World Conditions: Virtual testing under various operating conditions helps identify potential issues before physical prototypes are made.
- Optimise Geometries: Parametric modeling allows for precise adjustments to piston features, enabling the fine-tuning of shapes for maximum efficiency.
- Integrate Material Properties: CAD tools can incorporate material data, helping engineers select the best materials to balance performance, cost, and manufacturability.
Benefits of Performance-Driven Design
Adopting optimised CAD design for automotive pistons enhances efficiency, accelerates development cycles, and yields numerous advantages:
- Enhanced Engine Efficiency: Optimised pistons contribute to better combustion, reducing fuel consumption and emissions.
- Improved Reliability: Designs that account for stress distribution and thermal expansion reduce the risk of piston failure.
- Accelerated Development Cycles: Automation and simulation reduce the need for physical prototypes, speeding up the design process.
By focusing on performance from the outset, engineers can create pistons that meet stringent industry standards while satisfying consumer demands for efficiency and reliability.

Our Automated Solutions for Piston Design
Our Expertise in Automation
At Transient Geometry, we harness the power of automation to transform the piston design process. Our solutions offer:
- Parametric Modeling Automation: We develop parametric models that allow for quick adjustments of key design parameters such as crown shape, skirt profile, and ring groove placement. This flexibility enables rapid exploration of design variations.
- Automated Simulation Workflows: Our tools automatically set up and run simulations for each design iteration, evaluating performance metrics like stress distribution, thermal behavior, and deformation under load.
- Optimisation Algorithms: Utilising advanced algorithms, including artificial intelligence and machine learning, we identify optimal design configurations that meet or exceed performance criteria.
Detailed Workflow of Our Automated Design Process
- Client Consultation and Requirement Gathering
- We begin by understanding the client’s specific needs, including performance targets, material preferences, and manufacturing constraints.
- Development of a Parametric CAD Model
- Our engineers create a detailed parametric model of the piston, defining variables for critical dimensions and features.
- Design Space Exploration
- Using our automation tools, we generate a wide range of design variants by adjusting parameters within defined limits. This process allows for the evaluation of thousands of potential designs.
- Automated Simulation and Analysis
- Each design variant undergoes rigorous simulation tests. We analyse:
- Structural Integrity: Finite Element Analysis (FEA) assesses stress and strain under operating conditions.
- Thermal Performance: Thermal simulations evaluate heat distribution and potential hotspots.
- Dynamic Behavior: Kinematic simulations examine the piston’s motion and interaction with other engine components.
- Optimisation and Selection: Results from the simulations are compiled, and optimisation algorithms identify designs that offer the best balance of performance, reliability, and manufacturability.
- Each design variant undergoes rigorous simulation tests. We analyse:
- Client Review and Finalisation
- We present the top-performing designs to the client, incorporating feedback to finalise the piston design.
Advantages of Partnering with Transient Geometry
Efficiency and Speed
Our automated solutions drastically reduce the time required for piston design:
- Rapid Prototyping: Virtual simulations eliminate the need for multiple physical prototypes.
- Accelerated Decision-Making: Access to comprehensive data enables quicker selection of optimal designs.
Enhanced Accuracy and Quality
By minimising manual intervention, we reduce the potential for errors:
- Consistent Results: Standardized processes ensure that every design iteration is evaluated using the same criteria.
- Data-Driven Insights: Detailed analytics provide a deeper understanding of how design changes affect performance.
Cost Savings and ROI
Our approach leads to substantial financial benefits:
- Reduced Development Costs: Fewer physical prototypes and shorter development cycles lower expenses.
- Faster Time-to-Market: By adopting optimized CAD design for automotive pistons, our clients achieve faster time-to-market and reduced costs.
Future-Proofing Your Engine Designs
Adapting to Industry Trends
The automotive industry is rapidly evolving, with increasing emphasis on:
- Emission Reduction: Stricter regulations require engines that produce fewer emissions. Our optimised piston designs contribute to cleaner combustion.
- Electrification and Hybrid Systems: As the industry shifts towards electric and hybrid vehicles, specialized piston designs are needed for engines that operate under different conditions. Our tools are adaptable to these new requirements.
Continuous Improvement and Innovation
We are committed to staying at the forefront of technology:
- Research and Development: We continually refine our algorithms and methods to incorporate the latest advancements in engineering and materials science.
- Scalable Solutions: Our tools are designed to grow with your business, accommodating increasing complexity and volume.
Your Next Steps
Ready to explore how optimized CAD design for automotive pistons can revolutionise your processes? Contact Transient Geometry today to discover how our automated solutions can enhance efficiency, reliability, and profitability in your engine component designs.
If you want to find out more about how you can automate the creation of multiple variants then why not check out Automating data entry in Inventor with Excel.
Leave a Reply